New CFD Model Optimizes Green Production of High-Purity Chemicals
Published 10 April, 2025
In the production of dimethyl carbonate (DMC), a versatile chemical critical for manufacturing lithium-ion battery electrolytes, pharmaceuticals and high-performance polymers, an ultra-high purity (≥99.95%) is needed to meet stringent industrial standards. Melt crystallization, as a green manufacturing method is highly important for this purpose; however, the widespread adoption of this technology has been hindered by complex heat and mass transfer phenomena, which can lead to uneven crystal growth and suboptimal yields.
Addressing these challenges, a research team from Tianjin University’s National Engineering Research Center of Industrial Crystallization Technology has proposed a new computational model that reveals the dynamics of DMC crystallization. By integrating computational fluid dynamics (CFD) simulations with experimental data, the team mapped how natural convection—a process driven by temperature-induced fluid flow—shapes the distribution of DMC crystal layers, causing lower yield.
“The dynamic heating strategy precisely modulates the temperature gradient along the crystallizer walls, providing a balance between rapid crystal growth and higher yield,” explains explained lead author Prof. Hongxun Hao. “Our model bridges the gap between theoretical predictions and industrial reality.”
By quantifying how fluid dynamics interact with thermal gradients, the researchers can now tailor crystallization processes to specific materials, slashing energy use and production time without compromising quality.”
The study further introduced a predictive correlation that links crystallization time, crystal yield, and heat transfer coefficients—a tool provided a new sight of design and optimization of melt crystallization processes. The findings are published in Green Chemical Engineering.
“Validated through laboratory-scale experiments, the computational framework offers a cost-effective pathway for scaling up melt crystallization in industries,” adds Hao. “Beyond DMC, the methodology holds promise for purifying other thermally sensitive materials, such as organic semiconductors and pharmaceutical intermediates, where precision and sustainability are paramount.”
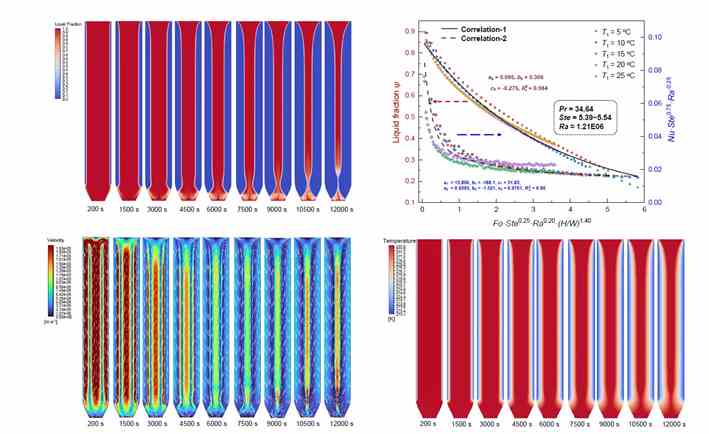
Contact author details: Hongxun Hao National Engineering Research Center of Industrial Crystallization Technology, School of Chemical Engineering and Technology, Tianjin University, Tianjin, China, Email: hongxunhao@tju.edu.cn
Funder: This research was supported by National Natural Science Foundation of China (Grant number U22A201195) and the High-end chemicals and cutting-edge new materials Technology Innovation Center of Hefei (Grant number ECEC-HCHC202208).
Conflict of interest: The authors declare that they have no known competing financial interests or personal relationships that could have appeared to influence the work reported in this paper.
See the article: M. Chen, J. Li, J. Qian, Y. Wu, X. Xu, M. yuan, T. Wang, N. Wang, X. Huang, H. Hao, Numerical Simulation and Optimization of Dimethyl Carbonate Melt Crystallization Based on Computational Fluid Dynamics, Green Chemical Engineering, https://doi.org/10.1016/j.gce.2025.01.005