Theoretical design and experimental verification of high-entropy carbide ablative resistant coating
Published 03 July, 2024
The hot-end components of high-performance high-speed aircrafts need to meet performance requirements such as long service life, wide temperature range oxidation resistance and ablation resistance. This puts forward higher requirements for high-temperature service performance of thermal protection system (TPS).
With low density, low expansion and excellent high temperature mechanical properties, carbon-carbon (C/C) composites are expected to be the best choice for the new generation of TPS. However, the oxidation sensitivity of C/C composites severely limits their service life in high-temperature ablation environment. It is effective for coating technology to enhance the ablation resistance of C/C composites. High-entropy carbide coatings with high melting points and excellent ablation resistance have become the focus of researchers.
Traditionally, the carbide coating design typically begins with the direct manipulation of carbide elements, with the carbide constituents expected to generate oxide components passively. This forward design methodology neglects to incorporate a direct compositional strategy for the oxide scale, which plays a crucial role in the high-temperature performance for carbides ceramic coatings.
A stable surface oxide scale is the key to ensure the long-term ablation of high-entropy ceramics, as it acts as a barrier between oxygen and the unoxidized high-entropy ceramics. Neglecting the composition design of the oxide scale will limit the high-temperature service life of high-entropy carbides.
In a study published in the KeAi journal Advanced Powder Materials, a team of researchers from Northwestern Polytechnical University in Xi'an, China, proposed the concept of inverse design to break such a limitation on high-entropy carbides.
“Firstly, the composition of high-entropy oxide scale with excellent thermal stability is designed. Then, the high-entropy carbides are inversely designed, enabling the designed high-entropy oxide scale to form in-situ on their surface during the ablation processes, thereby enhancing their ablation resistance,” shares the study’s senior and corresponding author Jia Sun.
The researchers designed (Hf0.36Zr0.24Ti0.1Sc0.1Y0.1La0.1)C1-δ (HEC) coatings using the inverse theoretical method and validated through ablation resistance experiments. The linear ablation rate of the HEC coatings was measured at -1.45 μm/s, which is only 4.78% of that of pristine HfC coatings after oxyacetylene ablation at 4.18 MW/m2, demonstrating excellent ablation resistance. HEC coatings also exhibit higher toughness, with a Pugh’s ratio of 1.55 compared to HfC 1.30.
“During ablation, a dense (Hf0.36Zr0.24Ti0.1Sc0.1Y0.1La0.1)O2-δ oxide scale forms in-situ on the surface, contributing significantly to improved anti-ablation performance due to its high phase and structural adaptability, with a lattice constant change not exceeding 0.19% at 2000–2300 °C,” adds Sun.
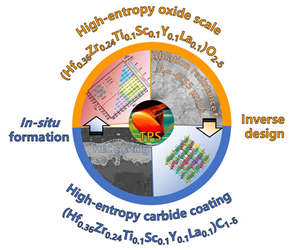
Contact author details:
Jia Sun (j.sun@nwpu.edu.cn)
Science and Technology on Thermostructural Composite Materials Laboratory, Shaanxi Key Laboratory of Fiber Reinforced Light Composite Materials, Northwestern Polytechnical University, Xi'an, 710072, China
Funder:
This work is supported by the National Key R&D Program of China (2022YFB3708600, 2021YFA0715802), Aeronautical Science Foundation of China (2022Z055053004), Fund of Key Laboratory of National Defense Science and Technology (WDZC20235250505) and National Major Science and Technology Projects of China (J2022-VI-0011-0042).
Conflict of interest:
The authors declare that they have no known competing financial interests or personal relationships that could have appeared to influence the work reported in this paper.
See the article:
Guo Lingxiang, et al. Theoretical design and experimental verification of high-entropy carbide ablative resistant coating. Advanced Powder Materials, Volume 3, Issue 5, 2024, pages 100213. https://doi.org/10.1016/j.apmate.2024.100213